General Glass Handling & Safety Tips
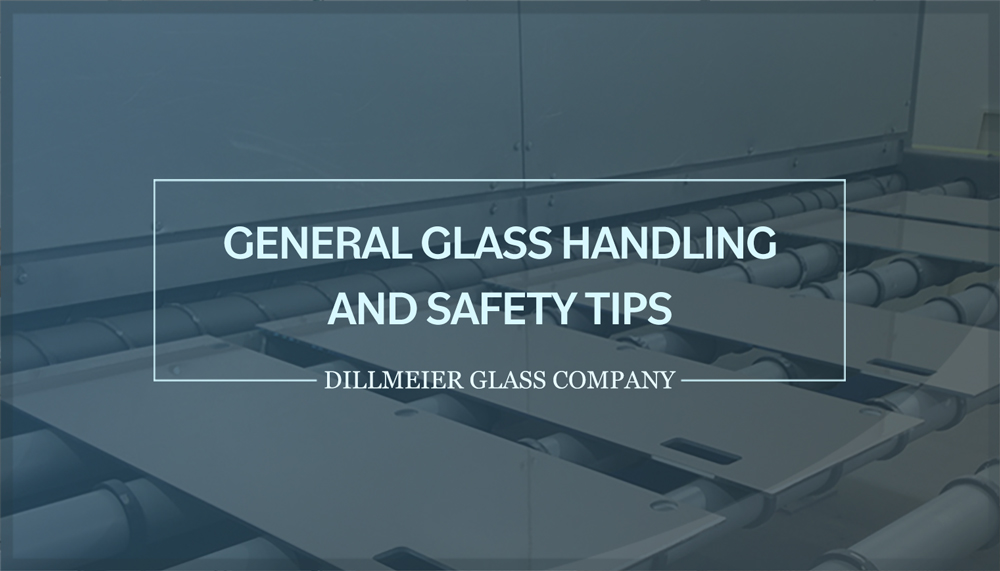
Commercial glass manufacturers and fabricators must take the time to educate both their employees and customers about general glass handling and safety precautions. Doing so not only helps reduce the risk of glass breakage and injuries on the job, but also reassures customers that the company makes the handling of their custom product and safety top priorities.
First Things First: Tempered Glass Breakage Is Uncommon, but Not Impossible
The majority of manufactured glass products undergo a tempering process before completion. Tempered glass, also called safety glass, is more than four times stronger than annealed glass.
At Dillmeier Glass Company—a fourth-generation glass fabricator whose tempering process is certified annually by the nonprofit Safety Glazing Certification Council (SGCC)—annealed glass is measured, heated in a tempering oven, cut and cleaned. The glass is baked to approximately 1,200 degrees Fahrenheit before quickly cooled via blasts of cold air—a process known as “quenching.” This creates stress, and thus, tension, inside the glass, while the outside is compressed, making the material stronger and safer to handle.
If by some chance the glass breaks, it does so in small pieces—far safer than the shards created by annealed glass.
Reasons for Tempered-Glass Breakage can Include:
- Damages, such as scratches and chips to the glass. This can result in spontaneous glass breakage in the future. For example, care should be taken while cleaning glass, as it is susceptible to movement. The corners and edges coming in contact with anything can cause damage, which can then lead to breakage.
- Improper moving or handling of glass. If glass comes into contact with a hard or sharp object when being handled, it can get scratched or chipped, breaking spontaneously. Furthermore, large pieces of glass improperly moved can also break.
- Nickel sulfide inclusions. International standards organization ASTM International’s C 1048 guidelines permit blemishes in glass, including nickel sulfide, between 0.020 and 0.100 of an inch, depending on glass size. Such inclusions could cause spontaneous glass breakage, but there isn’t any known technology completely eliminating their formation in float glass. These can be so small that there isn’t a practical way to inspect for their presence. Consequently, U.S. float glass manufacturers have worked hard and have virtually eradicated this element from their production facilities.
Following Glass Handling & Safety Tips Can Be Critical for Manufacturers & Fabricators
Managing glass comes with inherent risks, but adhering to proper safety protocols and handling guidelines can mitigate accidents and prioritize the well-being of employees.
Here are some suggestions to consider:
- Carry glass to your side with two hands.
- Never carry glass under your arm or above your head.
- Always use two team members to move large sheets of glass.
- Use proper hand and body position such that you are not in the “line of fire” in the event of breakage.
- Replace worn safety equipment before performing the job.
- Do not stand or walk on broken glass.
- Never break glass into smaller pieces with your foot or hand.
- Do not hold on to broken glass or try to stop falling glass; move out of the way to a safe location.
- Do not reach or catch glass by the corner of the lite.
- Always be aware of your and other team members’ surroundings.
- Inspect containers and glass before unpacking, which is essential to reducing potential hazards.
- Ensure that no team members are in the area of glass movement.
- Do not stand on racks.
- Ensure that glass is strapped to the rack before moving it.
- Observe strapping for wear and replace if necessary.
- Be aware of forklift truck traffic and never stand in front of any container or rack of glass when it is being moved or being set down. Verify that the rack is secure.
- Wear proper safety equipment such as hearing protection, gloves, safety shoes, and masks in edge deletion and glass-cutting operations.
- When setting the glass on the floor, place the long side of the glass first, and use soft or padded surfaces such as blankets or other cushioning agents to keep the glass safe.
- When working with glass, it is essential to have a medical professional or a paramedic team on standby at all times to address any unforeseen emergencies. Additionally, all workers should undergo training in administering first aid to their colleagues.
Offering comprehensive training, utilizing appropriate tools and equipment, and adhering to safety guidelines and regulations are crucial steps in averting injuries and minimizing the potential for glass damage.
Trust Dillmeier for Your Glass Fabrication Needs
No matter what your specific requirements or applications are, work with Dillmeier Glass Company for an industry-leading glass fabricator with unmatched quality, innovation, and personalized solutions tailored to elevate your spaces and projects.
Our commitment to excellence and a seamless collaborative approach ensures that every piece of glass we craft is a testament to precision, durability, and aesthetic brilliance.
At Dillmeier Glass, our decades-long expertise in the industry sets us apart as leaders in bespoke glass solutions. Collaborate with our seasoned team of professionals who specialize in translating your vision into reality. From concept to installation, our craftsmen ensure precision and attention to detail, delivering glass creations that not only meet but exceed your expectations.
Explore the endless possibilities of our customizable glass offerings and let us elevate your project to new heights. Contact Dillmeier today to learn what we can do for you!