Glass Tempering
for Added Safety, Strength & Durability
Protecting your project glass from buckling, cracking, and shattering under pressure
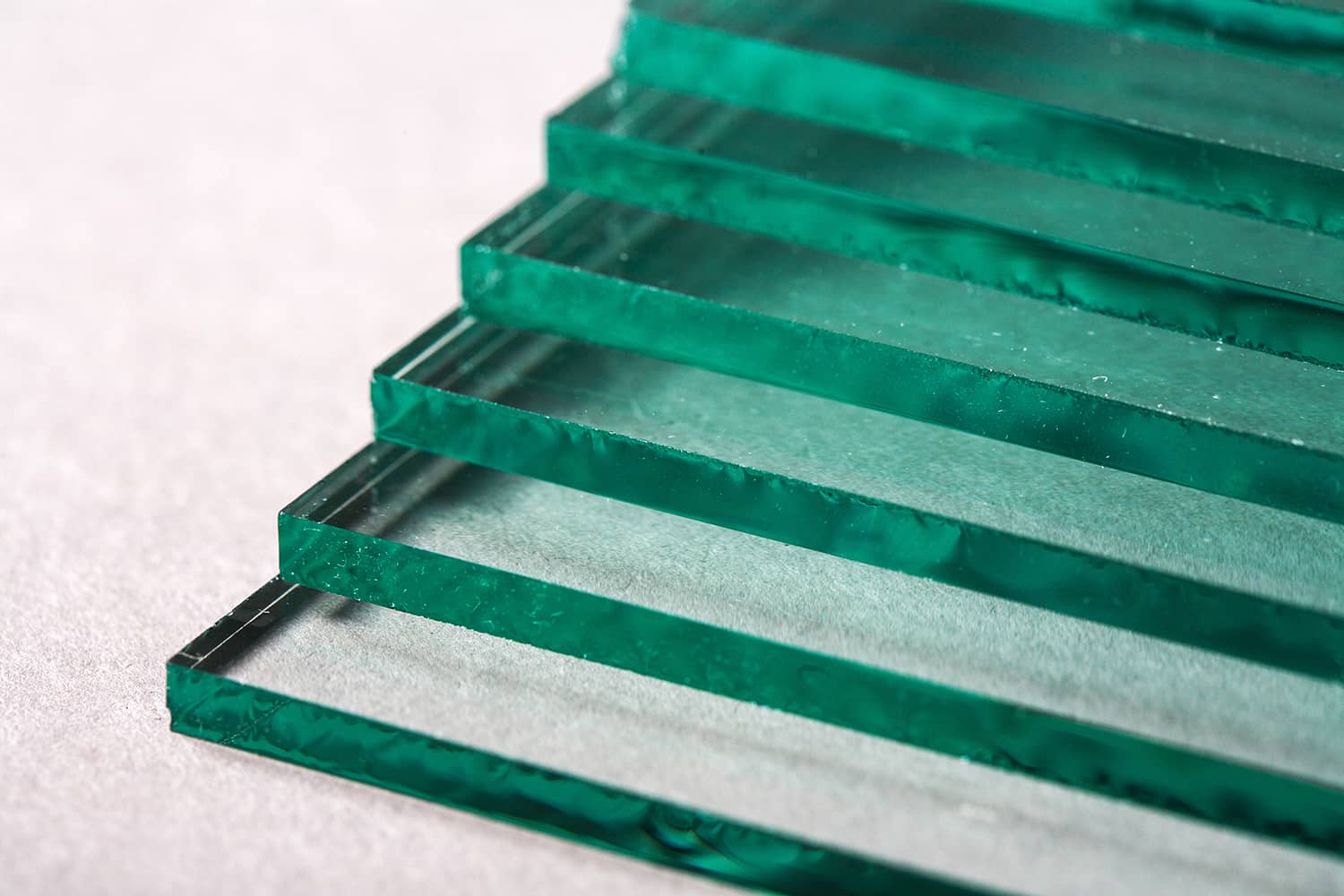
When planning your glass project, you never want to worry about possible breakage.
Due to its safety-concentrated properties, tempered glass fosters strength and durability, reducing the likelihood of warping, cracking or shattering under any circumstances. However, if an issue should ever occur, tempered glass separates into harmless, pebble-like pieces, rather than jagged slivers with sharp edges. These attributes are even more paramount for high-traffic applications such as entrance doors, railings and display cases, as well as office walls, partitions, and dividers.
A Standards-Based Process
Occurring post-fabrication, our tempering process is built on standards set forth by ASTM International. These include important elements such as correct countersink, notch and hole placement, as well as glass thickness and sizing, edge distance requirements, and minimum widths.
After your glass is cut and shaped to your specifications, it is inspected, washed, and placed within our in-house tempering ovens, which boast industry-standard temperatures of more than 600 degrees Celsius (1,112 degrees Fahrenheit). The heated glass then undergoes high-pressure cold air blasts, causing the outer layers to cool and contract faster than the interior, creating tension between the layers. As this pressure increases, the glass becomes stronger and less likely to break.
Safest Production Standards For Highest Assurance.
A designated Safety Glazing Certification Council (SGCC)-certified tempering company, such as Dillmeier Glass can help to ensure your materials are handled in line with best practices to ensure consistent production standards even for specialist projects, including:
- Specifications that are outside the ASTM tempering guidelines
- Uncertainty over specifications and requirements, including glass thickness and hole placement
- Customized solutions such as slotted glass, relief cuts, pre-purchased specific hardware, and other project adjustments.