How to UV Bond Glass
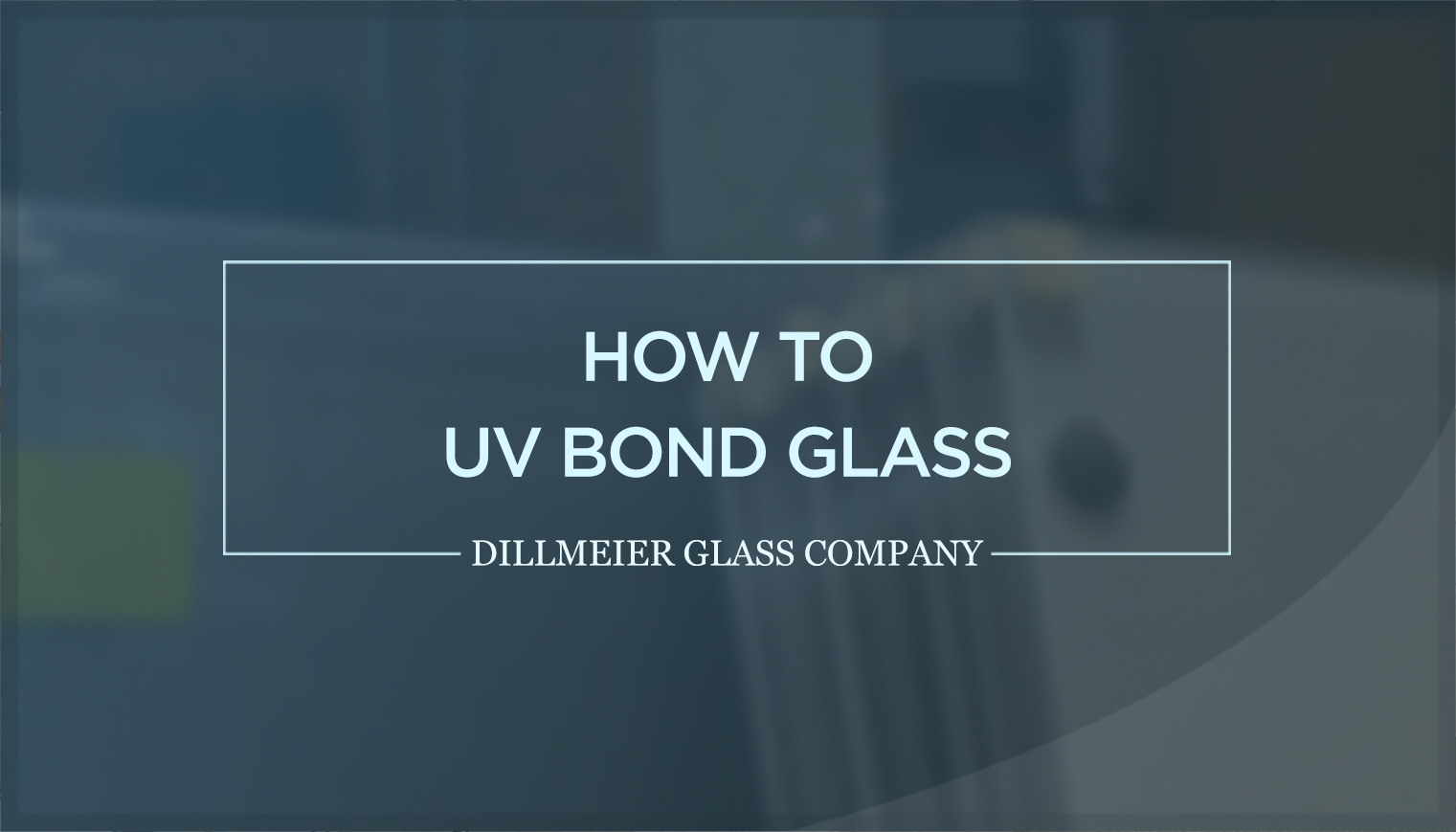
Editor’s Note: This blog post was originally published in March 2020 and has been revised to reflect industry updates.
Ultraviolet (UV) bonding involves the preparation and joining of two glass pieces utilizing a specialized, two-step adhesive process of pre-curing and final curing.
When successful, the UV bonding adhesive should be minimally visible, with smooth and clean lines. This is used frequently for retail applications, such as creating frameless glass display cases. Despite involving several pieces of glass, UV bonding produces an elegant and seamless display.
Before discussing how UV bonding can achieve a desirable appearance, let’s first address its relevant applications, security features, and more.
Suitable UV Bonding Applications
UV bonding is most helpful with strong, clear adhesive for retail showcases, furniture, and other decorative glass pieces. It can also be bonded with metal hardware— specifically knobs, locks, and hinges.
UV Bonding Security Features
UV bonding is most helpful with strong, clear adhesive for retail showcases, furniture, and other decorative glass pieces. It can also be bonded with metal hardware— specifically knobs, locks, and hinges.
Transparent, UV-bonded display cases are sometimes targets of smash-and-grab crimes, in which perpetrators strike them with hammers and steal high-end merchandise before running for the exits.
Dillmeier Glass Company has developed a process to thwart these crimes, whereby every pane and case is securely fastened. This makes smashing more difficult, while still maintaining a display case’s decorative brilliance and elegance.
How Strong Is UV Bonding?
One of the most powerful adhesives, UV glue supports larger surfaces than alternative methods, and results in fewer instances of breakage.
The UV Bonding Process
Choosing Materials
Dillmeier Glass Company recommends low-iron glass with flat-polished edges for UV bonding—both providing a finished appearance for retail display cases and furniture pieces.
Note the following UV bonding success guidelines:
Specific Glass Components
All post-tempered glass components should be completely flat, with a limited bow. Tempered and mirrored glass boast high strength and low UV absorption, with permeability dependent upon thickness and color.
UV Bonding Combinations
Self-stabilizing construction is preferred when bonding glass with glass to avoid high-bending tensions, and withstand greater loads.
UV bonding glass to metal and glass to glass features UV-stabilized, yellowing-resistant properties providing permanent transparency, the highest level of clarity, and strongest adhesion.
Laminated Glass
With edge interlayers presenting additional challenges, laminated glass is best UV bonded by a fabricator boasting specialized equipment and experienced operators, such as Dillmeier Glass Company.
Decorative Glass
Weaker surfaces such as ornamental, wired, or sandblasted glass could require specialized adhesives.
Surface Preparation
Surfaces should be clean and residue-free for maximum adhesion. It’s also recommended to wear UV-protective glasses and synthetic-based disposable gloves.
When bonding metal to glass, consider stainless steel for its strength. All surfaces must be free of natural separating agents such as greases and oils, which could interfere with the process.
It’s also important to work with a fabricator utilizing a clean, climate-controlled room devoid of contaminants such as chemical vapors, dust, and aerosol particles.
Adhesive Selection
UV adhesives comprise acrylate- or epoxy-based resins that polymerize with curing through UV light. These are generally utilized in an industrial setting. Selecting the right adhesive depends on the types of materials bonded, conditions, and temperature.
UV adhesives set when exposed to light from special, UV-curing lamps. Transparent adhesion occurs when the bonded materials harden, and glass to glass and glass to metal.
Adhesive Application
Once all materials are securely fastened and properly fitted, add a fixing aid to hold the glass in place through suction pads for positioning and support. This is especially important for high-end applications requiring extra attention to detail, such as retail glass display cases and shelving.
The adhesive should be applied shortly after heating the bonding area, and completed before or after joining the glass.
UV Curing
Note the following pre-curing and final curing steps. It’s also recommended to perform test bondings for quality assurance.
- Pre-curing requires between 10 seconds and two minutes, depending on the UV lamp used and its effectiveness. Any residues and excess adhesive should be removed at this time.
- Final curing lasts one to five minutes and is dependent on lamp type.
- For best results and even curing, the UV lamp should be placed close to glass edge.
When bonding metal to glass, consider stainless steel for its strength. All surfaces must be free of natural separating agents such as greases and oils, which could interfere with the process.
Safe Shipping & Transport
It’s essential to transport finished UV-bonded casework safely and securely to prevent damage. Dillmeier Glass Company has perfected custom packing and crating, supporting its weakest points and ensuring the reliable shipment of thousands of UV-bonded glass projects—with a breakage rate of less than 1 percent!
If UV bonded cases are kept in a below-freezing state for extended periods, they risk cracking. To avoid damage from drastic temperature swings during shipment, we utilize custom hot packs during the winter to maintain optimal temperatures.
Achieving a Specific Appearance
With UV bonding a highly specialized process, it’s best to work with a reputable glass fabricator and relevant partners for best results.
Contact Dillmeier Glass Company to learn how we can help with your UV bonding project.